Секреты алмазного сверления: Как выбрать идеальный инструмент
Сварка ТИГ: в чём отличие от других методов сварки
Винтовые компрессоры: как выбрать надежное оборудование для производства
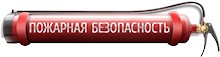

→ Винтовые компрессоры: как выбрать надежное оборудование для производства
Винтовые компрессоры: как выбрать надежное оборудование для производства
Оценка потребности в сжатом воздухе и требований к качеству
Если вам срочно требуется купить винтовой компрессор, перед выбором необходимо точно определить потребность производства в сжатом воздухе. Это ключевой фактор‚ влияющий на выбор оборудования. Для этого суммируйте потребление воздуха всеми пневматическими устройствами‚ добавив 15-20% запаса на утечки и возможное расширение производства. Например‚ при общей потребности 50 м3/час‚ компрессор должен обеспечивать не менее 0‚85 м3/мин (50/60*1.15).
Кроме количества‚ важно качество сжатого воздуха. ГОСТ Р ИСО 8573-1-2016 регламентирует допустимые уровни загрязнений. Учитывайте требования вашего оборудования к чистоте‚ влажности и содержанию масла в воздухе. Это обеспечит стабильную работу и продлит срок службы пневматической системы.
Принцип работы и основные компоненты винтового компрессора
Винтовой компрессор‚ в отличие от поршневого‚ сжимает воздух не за счет возвратно-поступательных движений поршня‚ а посредством вращения двух винтов особой формы‚ расположенных внутри корпуса. Этот механизм обеспечивает непрерывный поток сжатого воздуха‚ что является ключевым преимуществом для многих производственных процессов.
Основные компоненты винтового компрессора и их взаимодействие:
- Винтовой блок: Сердце компрессора. Два ротора (винты) вращаются навстречу друг другу‚ уменьшая объем между ними и сжимая поступающий воздух. Один из роторов – ведущий‚ второй – ведомый. Профиль винтов обеспечивает эффективное сжатие с минимальными потерями.
- Приводной двигатель: Обеспечивает вращение винтового блока. Может быть электрическим‚ дизельным или‚ реже‚ бензиновым. Выбор типа привода зависит от условий эксплуатации и требований к мощности.
- Впускной клапан: Регулирует объем воздуха‚ поступающего в винтовой блок. Управляется пневматической системой и реагирует на изменения давления в системе.
- Система смазки: В маслозаполненных компрессорах масло впрыскивается в винтовой блок. Оно выполняет несколько функций: уплотняет зазоры между винтами‚ охлаждает сжимаемый воздух и смазывает вращающиеся детали. В безмасляных компрессорах смазка не используется‚ что обеспечивает более высокую чистоту сжатого воздуха.
- Масляный сепаратор (для маслозаполненных компрессоров): Отделяет масло от сжатого воздуха. Эффективность сепаратора критически важна для качества конечного продукта.
- Воздушный фильтр: Очищает всасываемый воздух от пыли и других загрязнений‚ защищая винтовой блок от износа.
- Система охлаждения: Отводит тепло‚ выделяющееся при сжатии воздуха. Может быть воздушной или водяной. Эффективное охлаждение повышает надежность и производительность компрессора.
- Ресивер: Ёмкость для хранения сжатого воздуха. Сглаживает пульсации давления и обеспечивает резерв воздуха для кратковременных пиковых нагрузок.
- Система управления: Контролирует работу компрессора‚ поддерживая заданное давление и обеспечивая защиту от перегрузок.
Принцип работы:
Воздух поступает через впускной фильтр и попадает в винтовой блок. Вращение винтов уменьшает объем воздушной камеры‚ сжимая воздух и повышая его давление. В маслозаполненных компрессорах в винтовой блок одновременно впрыскивается масло. Смесь сжатого воздуха и масла поступает в масляный сепаратор‚ где масло отделяется и возвращается в систему смазки. Очищенный сжатый воздух поступает в ресивер и далее к потребителям. Система управления контролирует давление в ресивере и регулирует работу впускного клапана‚ поддерживая заданный уровень давления.
Понимание принципа работы и основных компонентов винтового компрессора поможет вам выбрать оборудование‚ наиболее подходящее для ваших производственных задач и обеспечивающее надежную и эффективную работу пневматической системы.
Производительность винтового компрессора: расчет и единицы измерения
Производительность винтового компрессора — это объем воздуха‚ который он может сжать за единицу времени. Правильный расчет этого параметра критически важен для обеспечения эффективной работы пневматического оборудования и предотвращения простоев производства. Недостаточная производительность приведет к падению давления в системе‚ а избыточная — к неоправданным затратам на электроэнергию.
Единицы измерения:
Производительность обычно измеряется в кубических метрах в минуту (м3/мин) или литрах в минуту (л/мин). При выборе компрессора важно обращать внимание на то‚ какая именно производительность указана: на входе (всасывание) или на выходе (нагнетание). Производительность на выходе всегда меньше из-за потерь при сжатии. Рекомендуется ориентироваться на производительность на входе‚ которая также иногда называется «эффективной производительностью» или FAD (Free Air Delivery).
Расчет производительности:
Для определения необходимой производительности компрессора нужно суммировать потребление воздуха всеми пневматическими инструментами и оборудованием‚ которые будут подключены к системе. Важно учитывать‚ что не все оборудование работает одновременно. Анализируйте циклы работы и пиковые нагрузки‚ чтобы получить реалистичную оценку. К полученному значению необходимо добавить запас 15-20% для компенсации возможных утечек в системе и будущего расширения производства.
Пример расчета:
- Пневмоинструмент 1: 200 л/мин
- Пневмоинструмент 2: 300 л/мин
- Пневматический станок: 500 л/мин
Общая потребность: 200 + 300 + 500 = 1000 л/мин
С учетом запаса 20%: 1000 * 1.2 = 1200 л/мин = 1.2 м3/мин
В данном случае потребуется компрессор с производительностью на входе не менее 1.2 м3/мин.
Дополнительные факторы:
Помимо суммарного потребления воздуха‚ на выбор производительности компрессора могут влиять и другие факторы:
- Режим работы: Для непрерывной работы рекомендуется выбирать компрессор с большей производительностью‚ чем для периодического использования.
- Тип оборудования: Некоторые виды пневматического оборудования требуют стабильного давления и большого объема воздуха‚ что необходимо учитывать при расчете.
- Климатические условия: В условиях высокой температуры окружающей среды производительность компрессора может снижаться.
Тщательный расчет производительности и учет всех факторов обеспечит эффективную и бесперебойную работу вашего производства‚ избегая проблем с падением давления или перерасходом электроэнергии. Не стесняйтесь консультироваться со специалистами‚ чтобы подобрать оптимальное оборудование для ваших конкретных нужд.
Рабочее давление: определение необходимого уровня и учет потерь
Рабочее давление — это давление сжатого воздуха‚ необходимое для корректной работы пневматического оборудования. Правильный выбор рабочего давления винтового компрессора так же важен‚ как и расчет производительности. Заниженное давление приведет к неэффективной работе инструментов и станков‚ а завышенное — к повышенному износу оборудования и увеличению энергопотребления.
Определение необходимого уровня давления:
Необходимый уровень рабочего давления определяется исходя из требований пневматического оборудования‚ которое будет использоваться. Эта информация обычно указывается в технической документации к оборудованию. Важно определить максимальное давление‚ требуемое каким-либо из инструментов или станков‚ поскольку компрессор должен обеспечивать этот уровень для всех потребителей.
Учет потерь давления:
При расчете рабочего давления необходимо учитывать потери‚ которые неизбежно возникают в пневматической системе. Эти потери связаны с трением воздуха о стенки трубопроводов‚ сопротивлением фитингов‚ фильтров‚ осушителей и других элементов системы. Чем длиннее трубопровод и чем больше в нем изгибов и соединений‚ тем выше потери давления.
Основные источники потерь давления:
- Трение в трубопроводах: Зависит от диаметра и длины труб‚ а также от скорости потока воздуха.
- Повороты и изгибы труб: Каждый поворот создает дополнительное сопротивление.
- Запорная арматура (краны‚ клапаны): Также вносит свой вклад в потери давления.
- Фильтры и осушители воздуха: Необходимы для очистки и подготовки воздуха‚ но создают дополнительное сопротивление.
Расчет давления с учетом потерь:
Для приблизительной оценки потерь давления можно использовать следующие значения:
- Поворот трубы на 90 градусов: 0.3 бар
- Осушитель воздуха: 0.5 ? 1 бар
Суммируйте потери давления на всех элементах системы и прибавьте эту величину к требуемому рабочему давлению оборудования. Полученное значение будет минимальным давлением‚ которое должен обеспечивать компрессор.
Пример расчета:
Требуемое давление оборудования: 6 бар
Потери в трубопроводе (2 поворота): 0.3 бар * 2 = 0.6 бар
Потери в осушителе: 0.7 бар
Минимальное давление компрессора: 6 + 1.3 = 7.3 бар
В данном случае следует выбирать компрессор с рабочим давлением не менее 7.3 бар. Рекомендуется добавить небольшой запас (0.5-1 бар) для обеспечения стабильной работы системы.
Правильный расчет рабочего давления с учетом потерь обеспечит эффективную и надежную работу пневматического оборудования и продлит срок его службы.
Требования к качеству сжатого воздуха: соответствие ГОСТ и контроль параметров
Качество сжатого воздуха играет решающую роль в надежности и долговечности пневматического оборудования‚ а также в качестве конечной продукции. Наличие загрязнений‚ влаги и масла в сжатом воздухе может привести к коррозии‚ засорению‚ преждевременному износу инструментов и механизмов‚ а также к браку продукции.
ГОСТ Р ИСО 8573-1-2016:
В России требования к качеству сжатого воздуха определяются ГОСТ Р ИСО 8573-1-2016. Этот стандарт классифицирует загрязнения по трем основным категориям:
- Твердые частицы: Пыль‚ окалина‚ продукты износа.
- Влажность: Содержание воды в сжатом воздухе.
- Масло: Остатки масла от смазки компрессора (для маслозаполненных моделей).
Стандарт устанавливает классы чистоты для каждой категории‚ от 1 (самый чистый) до 9 (самый загрязненный). Выбор необходимого класса чистоты зависит от требований конкретного оборудования и производственного процесса.
Контроль параметров качества:
Для обеспечения соответствия сжатого воздуха требуемым параметрам качества необходимо проводить регулярный контроль следующих показателей:
- Содержание твердых частиц: Измеряется с помощью специальных счетчиков частиц. Для достижения высокого класса чистоты используются фильтры различной степени очистки.
- Точка росы под давлением: Характеризует содержание влаги в сжатом воздухе. Чем ниже точка росы‚ тем меньше влаги. Для снижения влажности применяются осушители воздуха.
- Содержание масла: Измеряется в мг/м3. В безмасляных компрессорах содержание масла должно быть минимальным. В маслозаполненных компрессорах используются масляные сепараторы и фильтры для снижения содержания масла в сжатом воздухе.
Выбор оборудования для подготовки воздуха:
Для достижения необходимого класса чистоты сжатого воздуха используются различные фильтры и осушители. Выбор конкретного оборудования зависит от требуемых параметров и производительности компрессора.
- Фильтры: Предназначены для удаления твердых частиц и масла. Существуют фильтры грубой‚ тонкой и сверхтонкой очистки.
- Осушители: Снижают содержание влаги в сжатом воздухе. Различают рефрижераторные‚ адсорбционные и мембранные осушители.
Регулярное обслуживание:
Для поддержания качества сжатого воздуха на требуемом уровне необходимо проводить регулярное обслуживание компрессора и оборудования для подготовки воздуха. Это включает в себя замену фильтров‚ проверку работы осушителя и других компонентов системы. Своевременное обслуживание позволит избежать проблем с качеством воздуха и продлит срок службы оборудования.
Следование требованиям ГОСТ и регулярный контроль параметров качества сжатого воздуха обеспечат бесперебойную работу пневматического оборудования‚ повысят качество продукции и снизят затраты на обслуживание и ремонт.
Типы привода: прямой и ременной ? выбор оптимального варианта
Винтовые компрессоры могут оснащаться двумя основными типами привода: прямым и ременным. Каждый тип имеет свои преимущества и недостатки‚ и выбор оптимального варианта зависит от конкретных условий эксплуатации и требований к производительности‚ надежности и экономичности.
Прямой привод:
При прямом приводе вал двигателя напрямую соединен с валом винтового блока. Это обеспечивает максимальную эффективность передачи энергии и минимизирует потери мощности. Компрессоры с прямым приводом отличаются высокой надежностью и долговечностью‚ поскольку в них отсутствуют промежуточные элементы передачи‚ такие как ремни и шкивы.
Преимущества прямого привода:
- Высокий КПД и энергоэффективность.
- Повышенная надежность и долговечность.
- Компактные размеры.
- Низкий уровень шума.
Недостатки прямого привода:
- Более высокая стоимость.
- Меньшая гибкость в настройке скорости вращения;
Ременной привод:
При ременном приводе двигатель и винтовой блок соединены ремнем и системой шкивов. Этот тип привода позволяет изменять скорость вращения винтового блока‚ подстраивая ее под текущие потребности в сжатом воздухе. Ременной привод также обеспечивает некоторую защиту двигателя от перегрузок.
Преимущества ременного привода:
- Более низкая стоимость.
- Возможность регулировки скорости вращения.
- Защита двигателя от перегрузок.
Недостатки ременного привода:
- Более низкий КПД due to losses in the belt drive.
- Необходимость регулярной замены ремней.
- Более высокий уровень шума.
- Большие габариты.
Выбор оптимального варианта:
Выбор между прямым и ременным приводом зависит от следующих факторов:
- Режим работы: Для непрерывной работы и высоких нагрузок предпочтительнее прямой привод. Для периодической работы с переменной нагрузкой подойдет ременной привод.
- Требования к энергоэффективности: Прямой привод обеспечивает более высокую энергоэффективность.
- Бюджет: Ременной привод является более экономичным вариантом.
- Уровень шума: Прямой привод обеспечивает более тихую работу.
Резервирование: обеспечение бесперебойной работы производства
Для многих предприятий сжатый воздух является критически важным ресурсом‚ и его отсутствие может привести к остановке производства‚ финансовым потерям и срыву сроков поставок. Поэтому обеспечение бесперебойной подачи сжатого воздуха является первостепенной задачей. Одним из наиболее эффективных способов достижения этой цели является резервирование компрессорного оборудования.
Что такое резервирование?
Резервирование – это установка дополнительного компрессора или нескольких компрессоров‚ которые могут взять на себя нагрузку в случае выхода из строя основного оборудования. Это позволяет избежать полной остановки производства при аварии или плановом обслуживании основного компрессора.
Варианты резервирования:
- Полное резервирование: Установка резервного компрессора такой же мощности‚ как и основной. В случае выхода из строя основного компрессора‚ резервный полностью берет на себя нагрузку. Этот вариант обеспечивает максимальную надежность‚ но является наиболее затратным.
- Частичное резервирование: Установка резервного компрессора меньшей мощности‚ чем основной. В случае аварии резервный компрессор поддерживает работу наиболее критически важных участков производства‚ пока не будет восстановлена работоспособность основного компрессора. Этот вариант является более экономичным‚ чем полное резервирование‚ но обеспечивает меньшую степень защиты от простоев.
- Комбинированное резервирование: Использование нескольких компрессоров‚ работающих в параллель. В случае выхода из строя одного из компрессоров‚ остальные увеличивают свою производительность‚ компенсируя потерю. Этот вариант обеспечивает высокую надежность и гибкость‚ позволяя оптимизировать энергопотребление в зависимости от нагрузки.
Выбор варианта резервирования:
Выбор оптимального варианта резервирования зависит от следующих факторов:
- Критичность сжатого воздуха для производства: Чем важнее сжатый воздух для непрерывности производственного процесса‚ тем выше требования к надежности системы и тем более оправданным становится полное резервирование.
- Финансовые возможности: Полное резервирование является наиболее затратным вариантом‚ частичное – более экономичным.
- Возможность кратковременных остановок производства: Если допустимы кратковременные перерывы в работе‚ можно рассмотреть частичное резервирование.
Пример расчета резервной мощности:
Предположим‚ основное производство потребляет 10 м3/мин сжатого воздуха. Если остановка производства недопустима‚ необходимо полное резервирование – резервный компрессор мощностью 10 м3/мин. Если допустима частичная остановка менее важных участков‚ можно установить резервный компрессор мощностью‚ например‚ 5 м3/мин‚ обеспечивающий работу критически важного оборудования.
Резервирование – это инвестиция в надежность и стабильность вашего производства. Правильно подобранная система резервирования позволит избежать дорогостоящих простоев и обеспечит непрерывность работы предприятия.